Operators should be trained to spot signs that indicate stretch wrap machine repair is needed.
Operators should be trained to spot signs that indicate stretch wrap machine repair is needed.
Blog Article
A Comprehensive Strategy to Resolving Stretch Wrap Maker Repair Service Obstacles
You recognize that stretch wrap makers are crucial for preserving effectiveness in product packaging procedures. Issues can occur that interrupt performance. What are the ideal strategies to guarantee your makers run efficiently?
Recognizing Usual Stretch Cover Machine Issues
When you depend on stretch cover makers for effective packaging, it's essential to recognize common concerns that can interfere with operations - stretch wrap machine repair. One common problem is irregular stress, which can cause insufficient wrapping and endangered lots stability. If you notice the movie isn't sticking appropriately, check for damaged rollers or inappropriate settings
Another concern you may face is movie damage, typically caused by wrong film type or machine breakdowns. Consistently check the device for indicators of deterioration to stop this.
In addition, watch on film build-up or jams, which can halt manufacturing. Typically, this occurs because of misalignment or particles in the machine.
Last but not least, incorrect securing can result in lots coming apart throughout transit. Ensure your device is adjusted correctly to keep the integrity of your plans. By staying attentive and dealing with these concerns quickly, you can promote smoother operations.
The Value of Normal Precautionary Upkeep
Regular precautionary upkeep is important for maintaining your stretch cover device running efficiently and successfully. By routinely inspecting and servicing your tools, you can spot prospective concerns before they escalate right into expensive repair work. This aggressive approach not only prolongs the life-span of your machine but likewise assures that it runs at peak efficiency.
You should arrange routine examinations to tidy, lubricate, and replace worn elements. Maintaining your equipment adjusted aids maintain perfect wrapping high quality, minimizes waste, and boosts productivity. Additionally, documenting maintenance activities produces a trusted history that can inform future decisions.
Don't overlook the importance of training your staff on maintenance best practices. When everyone understands how to care for the device, you reduce the risk of operator mistake leading to breakdowns. Simply put, devoting to normal preventative upkeep is a wise investment that pays off in reduced downtime and improved performance in your procedures.
Fixing Methods for Quick Repair Works
Effective troubleshooting strategies can substantially minimize downtime when your stretch wrap machine encounters concerns. Begin by determining the symptoms. Is the equipment not covering correctly or is it making unusual sounds? When you've determined the issue, refer to the driver's manual for guidance on usual problems and solutions.
Following, inspect the machine's setups and controls; sometimes, a straightforward adjustment can settle the problem. Inspect the film stress and positioning, as inappropriate setup can bring about wrapping failings. Do not neglect electric connections; loosened or damaged cords can interrupt capability.
If you're still dealing with obstacles, take into consideration running diagnostic tests if your machine has that ability. Don't think twice to seek advice from with a professional if you can not resolve the issue quickly.
Training Operators for Effective Equipment Usage
To ensure your stretch wrap device operates at peak performance, correct training for drivers is vital. When operators understand the equipment's capabilities, they can maximize its potential and minimize downtime.
Encourage them to exercise under guidance, dealing with any inquiries or worries they may have. Frequently scheduled refresher course programs can keep their abilities sharp and assist them adapt to any kind of updates or modifications in technology.
In addition, impart a society of responsibility by empowering drivers to report problems or recommend enhancements. This proactive strategy not only boosts their confidence but likewise adds to the general efficiency of your procedures. With well-trained drivers, you'll see fewer mistakes and increased efficiency, ensuring your stretch wrap equipment stays a valuable possession.
Constructing a Strong Interaction Channel In Between Teams
Trained operators can just perform at their finest when there's a strong communication network in between teams. Efficient communication gets rid of misconceptions and guarantees everybody's on the very same page relating to equipment operations and repair service needs. Motivate routine check-ins and conferences to review problems, share understandings, and address concerns.
Using modern technology, like messaging apps or collaborative systems, can boost real-time interaction, making it simpler to report issues and share updates promptly. Appointing clear roles and obligations promotes liability, permitting team members to reach out to the ideal individual their website when concerns emerge.
Moreover, creating an open environment where everybody feels comfy sharing comments can bring about innovative remedies. By focusing on communication, you're not just enhancing equipment performance; you're also developing a cohesive team that functions together flawlessly. This joint spirit eventually brings about quicker repairs and minimized downtime, profiting the whole operation.
Spending in Quality Substitute Components
When it pertains to keeping your stretch cover makers, spending in high quality substitute parts is vital for making certain reliable efficiency and minimizing downtime. Low-cost choices may appear appealing, but they frequently lead to more substantial concerns down the line, costing you more out of commission and lost productivity. By selecting high-quality parts, you're not just taking care of a trouble; you're improving the general performance of your tools.
Furthermore, quality parts are typically get redirected here made to more stringent requirements, which indicates they'll fit far better and function more accurately. This lowers the chance of unanticipated breakdowns, permitting your operations to run efficiently. Additionally, trusted providers typically give service warranties, giving you comfort in your investment.

Evaluating Performance Information for Continual Renovation
To improve your stretch wrap maker's visit this website performance, you need reliable data collection strategies. By examining efficiency metrics, you can identify areas for enhancement and boost efficiency. Recognizing these opportunities not just improves procedures yet additionally lowers downtime and repair service costs.
Information Collection Strategies
Efficiency Metrics Assessment
While assessing performance metrics, it's crucial to focus on particular data factors that straight impact your stretch cover maker's performance. Beginning by tracking cycle times, as they reveal exactly how quickly your device runs under typical conditions. This continuous examination helps boost performance, decrease costs, and eventually boost your machine's longevity, leading to an extra reliable wrapping procedure in general.
Determining Renovation Opportunities
As you evaluate efficiency information, you can reveal beneficial improvement possibilities that boost your stretch wrap maker's performance. Look for patterns in downtime, cycle times, and cover quality. If constant malfunctions associate with certain operating problems, you can change procedures to reduce these problems.
Frequently Asked Questions
Just How Can I Inform if My Machine Demands a Repair Work or Just Maintenance?
To tell if your equipment requires fixing or just upkeep, listen for uncommon sounds, look for irregular efficiency, and inspect for visible wear. If concerns persist after maintenance, it's likely time for a repair service.
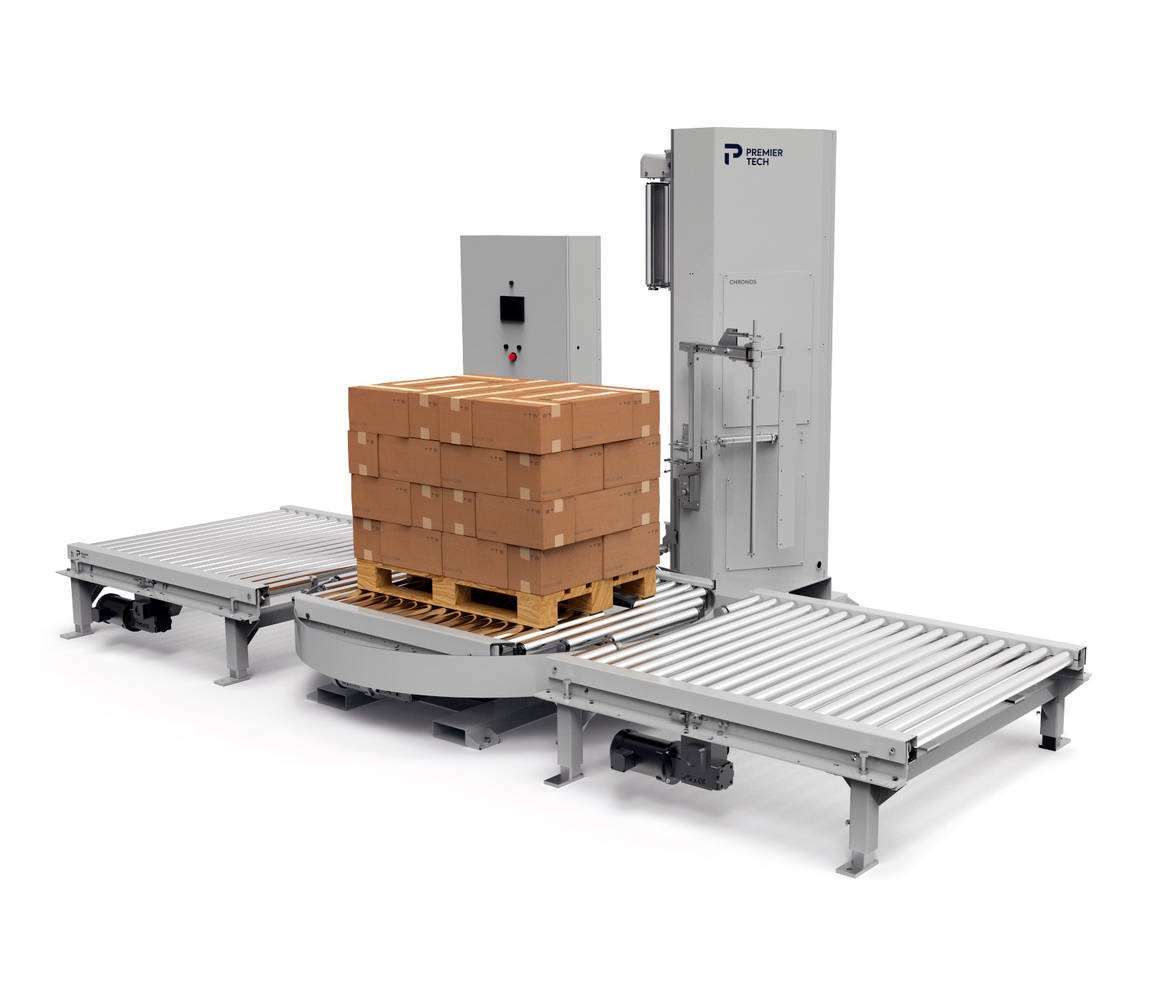
What Is the Typical Life Expectancy of a Stretch Cover Device?
The standard life expectancy of a stretch wrap device is usually five to 10 years, depending upon usage and upkeep. Normal care can expand its life, so watch on performance and address concerns quickly.
Are There Details Brands Understood for Better Integrity?
Yes, some brand names are known for their integrity. You'll locate that business like Signode and Lantech frequently receive favorable reviews - stretch wrap machine repair. Researching individual comments can help you pick a dependable stretch cover machine for your needs
What Are the Signs of Poor Operator Training?
If you see regular mistakes, inconsistent wrapping, or security incidents, those are indicators of bad operator training. Lack of comprehending concerning device features or failing to comply with protocols can considerably affect effectiveness and safety.
How Can I Locate a Competent Service Technician for Fixes?
To locate a certified specialist for repair work, ask for referrals from industry peers, check online testimonials, and verify certifications. You could additionally think about contacting neighborhood tools distributors that frequently have actually trusted service technicians available.
Conclusion
To sum up, taking on stretch wrap device repair work challenges needs a positive method. By focusing on preventive upkeep, offering thorough operator training, and buying top quality parts, you can substantially lower downtime and improve performance. Don't neglect the importance of strong communication between teams and constant analysis of maker result. By implementing these techniques, you'll not just boost wrapping high quality but additionally foster a society of effectiveness and renovation in your procedures. Remain ahead of issues prior to they arise!
Report this page